Wist u dat WITTENSTEIN ook Industrie 4.0 beleeft?
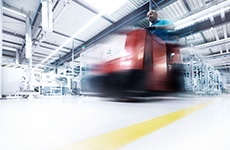
In principe gaat het erom de digitale wereld van gegevens, zoals die ook in systemen voor de productieplanning realiteit is, nauwer te vervlechten met de echte wereld van fysieke objecten zoals werkstukken, gereedschappen of werkstukdragers. Mensen, machines en producten moeten met behulp van zogenoemde cyberfysieke systemen (CPS) op een intelligente manier een netwerk vormen en voortdurend informatie met elkaar uitwisselen – en zo een vrijwel complete afspiegeling van actuele processen in real-time tot stand brengen.
De transparantie die door deze digitale koppeling ontstaat, is voorwaarde voor het nemen van gekwalificeerde beslissingen, het optimaliseren van processen en het voorkomen van de verspilling van waardevolle hulpbronnen. En voor het opbouwen en garanderen van een duurzame toekomst van een bedrijf. Want het gericht kanaliseren en gebruikmaken van de informatiestroom van goederenbewegingen is met het oog op actuele megatrends als productindividualisering, in extreme gevallen met partijgrootte 1, steeds grotere marktschommelingen en de in toenemende mate op globaal niveau georganiseerde productie op de lange termijn van levensbelang.
Demonstratiefabriek in Fellbach
Ongeveer twee jaar geleden is de “Urbane productie van de toekomst” van WITTENSTEIN bastian geopend. Hier wordt in het kader van het door het Duitse ministerie voor Onderwijs en Onderzoek gesubsidieerde onderzoeksproject “CyProS – Cyberfysieke productiesystemen” een aantal toepassingen uitgekozen en omgezet in een pilotproject. Dit vormde vanaf het begin een belangrijk onderdeel van de demonstratiefabriek. “Als aanjager van innovatie op het gebied van de mechatronische aandrijftechniek zien wij WITTENSTEIN ook als een wegbereider van Industrie 4.0. Centraal in onze activiteiten staan de productoptimalisatie en de ontwikkeling van producten die Industrie 4.0-ready zijn. De nieuwe concepten worden in Fellbach getest”, bevestigt dr. Jochen Schlick, hoofd van de innovatieve afdeling Cyber-Physical-Systems bij WITTENSTEIN. Twee toepassingen gingen onlangs van start: de “Optimalisatie van de intralogistiek” en de “Mobiele toegang tot informatie voor het bijhouden van de productieplanning”. In beide projecten wordt Industrie 4.0 verwezenlijkt door Auto-ID-technologieën, ingebedde systemen, IT-systemen voor de productie en de koppeling ervan binnen een fabrieksnetwerk. Op papier afgedrukte informatie maakt plaats voor digitale formaten, die afhankelijk van het gebruik en de taak in real-time ter beschikking staan en door de mens doelgericht en afgestemd op de situatie worden omgezet in geoptimaliseerde processen. Concreet wil dat zeggen dat bijvoorbeeld bij de productie verliezen kunnen worden vermeden die met de organisatie verband houden, bijvoorbeeld doordat materiaal niet op tijd aan machines wordt geleverd. Hierdoor wordt de totale productiviteit verhoogd.
De medewerker centraal
De rol van de mens als “meewerkende productiefactor en beslisser” wordt geherdefinieerd: “In de fabriek van de toekomst staat de mens centraal in de productie”. In plaats van de bediener wordt hij degene die wordt bediend. De machines leveren hem op het juiste tijdstip en op de juiste plaats informatie die voor zijn taken op maat is gesneden. De medewerker van morgen is planner en beslisser in een complexe omgeving. Daarmee worden hogere eisen aan zijn competenties gesteld”, legt prof. Dieter Spath, bestuursvoorzitter van WITTENSTEIN AG, uit. De rol van probleemoplosser blijft ook in deze nieuwe rolopvatting bestaan, “want ook in de wereld van Industrie 4.0 kunnen problemen met betrekking tot gereedschappen en processen ontstaan”, zegt dr. Maria Hergesell, hoofd technologiemanagement bij WITTENSTEIN bastian. “Dan zijn snelle en gekwalificeerde beslissingen vereist. En de mens kan die nog altijd het best nemen.”
Hiervoor heeft hij een volledig en actueel beeld van de voor hem relevante processen nodig, alsmede een tool om beslissingen te nemen en procedures te kunnen sturen. In de beide actuele projecten “Optimalisatie van de intralogistiek” en de “Mobiele toegang tot informatie voor het bijhouden van de productieplanning” zet men bij WITTENSTEIN bastian in op de nieuwste informatietechnologie: via WLAN gekoppelde tablets met speciaal hiervoor gemaakte “apps”. Deze uitrusting is niet alleen om technische redenen noodzakelijk, maar vormt voor de medewerkers ook een echte motivatie. “Nieuwe technologieën zoals tablets en smartphones bieden in vergelijking met traditionele media zoals planborden en insteekkaarten geheel andere mogelijkheden tot interactie – de nieuwsgierigheid naar en opgewondenheid over wat hier in de toekomst zal komen, is natuurlijk groot”, weet dr. Peter Stephan, projectleider binnen de innovatieve afdeling Cyber-Physical-Systems bij WITTENSTEIN.
Ontwikkeling in plaats van weerstand, acceptatie in plaats van afwijzing: de medewerkers zelf zorgen zo bij de verwezenlijking van Industrie 4.0 voor extra dynamiek, die al met al bij de verdere optimalisatie van processen alleen maar van nut kan zijn.
Optimalisatie van de intralogistiek: „Milkrun 4.0“
In de “Urbane productie van de toekomst” bij WITTENSTEIN bastian in Fellbach worden o.a. tandwielen geproduceerd. De besturing van de intralogistiek, d.w.z. het fysieke goederentransport tussen verschillende leverings- en afhaalterreinen, verliep tot dusver via “milkrun”: een logistiek medewerker rijdt ieder uur met een elektrische wagen voor intern transport door de fabriek. Deze relatief inflexibele cyclus reflecteert slechts tot op zekere hoogte de echte behoefte aan een optimale materiaaltoevoer, want aan het begin van de rit is nog niet duidelijk welke productieorders zich in welke toestand op welke plaats bevinden. Deze routine wordt momenteel in het kader van een Industrie 4.0-pilotproject door WITTENSTEIN bastian vervangen door een op de behoefte afgestemde materiaaltoevoer. Deze optimaliseert de voertuigbelasting, spaart hulpbronnen doordat het aantal te rijden trajecten wordt verminderd en flexibiliseert de levering van materiaal afhankelijk van de ordersituatie van dat moment. Hiertoe werd als eerste de echte wereld – orderdocumenten, werkstukdragers, leverings- en afhaalterreinen – van barcodes voorzien, die door machines konden worden geregistreerd. Het systeem voor de productieplanning en het bedrijfscontrolesysteem werden hieraan verbonden en de medewerkers uitgerust met scanners en tablets. Zij kunnen nu gegevens digitaal registreren en daarmee een transparant beeld krijgen van alle materialen in de productie: hiertoe leest de logistiek medewerker met behulp van de scanner en de app op de tablet de barcodes in de geleidepapieren van de uit te voeren productieorders in het planningssysteem in. Hetzelfde gebeurt met de codes van de afhaal- en leveringsterreinen. Op de achtergrond ontstaat zo een virtuele afspiegeling van de vereiste materiaalstroom. Deze wordt in een tweede stap omgezet in een rijroute met vertrektijden en stopplaatsen die op de tablet van de milkrun-chauffeur wordt weergegeven. Momenteel bevindt een intelligent planningsalgoritme zich in de testfase. Dit berekent de optimale rijtijden op basis van de virtuele afspiegeling van de vereiste materiaalstroom en het aantal rijopdrachten voor een dag. De eerste resultaten bevestigen al de eerder door een simulatie voorspelde optimalisatiemogelijkheden: de intelligente koppeling kan het aantal daadwerkelijk gereden transportcycli en trajecten voor de onderdelenbevoorrading bij de productie van tandwielen met tot wel 50 procent verminderen!
Mobiele toegang tot informatie
Het tweede pilotproject optimaliseert bij WITTENSTEIN bastian in Fellbach de organisatorische processen op het gebied van de productieplanning en -besturing. Ook hier ging het in principe erom de fysieke en de gegevenstechnische werkelijkheden met elkaar in overeenstemming te brengen. De bestaande conversieproblemen tussen de op insteekkaarten gebaseerde planbordsystemen op shop-floorniveau en de al geïmplementeerde productieplanning op basis van automatische gegevensverwerking had inhoudelijke en chronologische verschillen tussen beide werelden tot gevolg, wat in het echt tot afstemmingsproblemen en daarmee tot organisatorische verliezen vanwege niet-aanwezige of niet-actuele informatie leidde. Centraal in de Industrie 4.0-ready oplossing staat het digitale planbord, dat zowel is gekoppeld met de planningssoftware als met de mobiele tablets van de medewerkers. Hierdoor worden de conversieproblemen opgelost. Geen geplande order wordt meer tijdens het proces over het hoofd gezien of ongemerkt verplaatst en van een andere prioriteit voorzien. Planners en machineoperators werken met consistente en actuele, maar vooral met dezelfde gegevens. Wachtende orders kunnen mobiel op de machine worden opgeroepen en weergegeven. Via tablet en app kan de operator informatie over de bewerking van productieorders opvragen en eventuele problemen bij de orderbewerking, bijv. omdat een gereedschap niet paraat is, melden en multimediaal vastleggen. Uiteindelijk levert deze informatie ook belangrijke inzichten voor het continue verbeteringsproces.
Planning goed – processen goed – productie goed: ook dit project toont duidelijk de nuttige aspecten en potenties van Industrie 4.0!